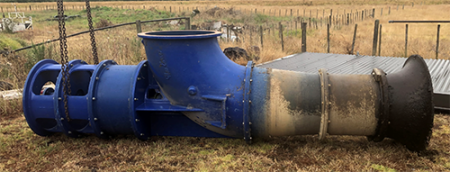
MacEwans PPF 24/30 pump out for inspection.
Not everybody realises it, but Waikato Regional Council owns and maintains an intricate network of pump and floodgate assets that help protect rural and urban areas from flooding. In the Lower Waikato catchment, our asset management team has been applying data to better assess the condition of our assets, which improves the reliability of the system and saves money on repairs and replacements at the same time.
The Lower Waikato flood protection scheme mitigates flood effects across thousands of acres of agricultural, horticultural and other productive lands, as well as the urban areas like Huntly. The system provides drainage where it is needed the most and works to channel the deluge of river water to the sea at Port Waikato during flood events.
Engineers create stopbanks by compacting earth along the river or stream bank to contain the flow of water, protecting land and property up to a designed limit. However, when it rains, the water on the land side of the stopbank still needs to make it into the river. When gravity can do the work, the system uses a floodgate. But where gravity works against the desired flow, the scheme uses 126 pump stations with 220 pumps to transport the water where it needs to be.
Maintaining the pumps is an ongoing process of monitoring, testing, repairing and replacing. This is where the team has put data to work, using advanced techniques such as vibration monitoring and thermography (heat detection) to evaluate the condition of the pumps and motors and make informed decisions about how long they should really last before they need overhauling.
Reliability Engineer Steve Hall says focusing on the asset condition rather than the manufacturers’ standard use by dates allows the team to safely and effectively extend the life of some assets, and accurately forecast earlier than expected failure on others. The team can repair these pumps in advance, which is also a simpler and more cost-effective job that reduces the risk of an unplanned pump failure. “We haven’t had an unplanned pump failure in this area over the last five years.”
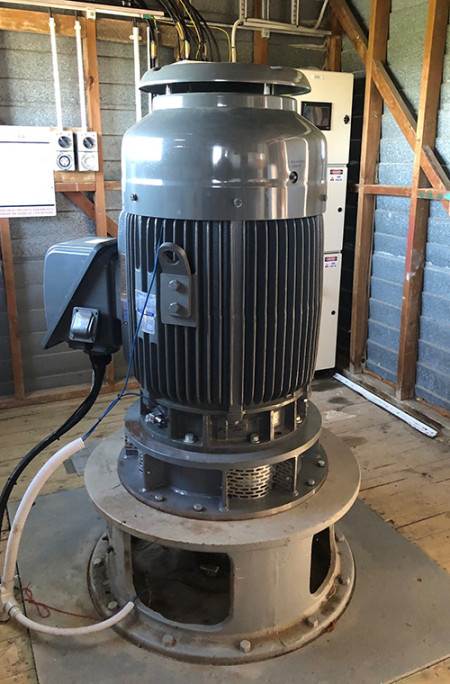
New pump motor ready to be installed.
Steve says it’s hard to determine exactly how much time this saves. However, asset breakdowns not only drain resources, but they also tend to happen at the most inconvenient times, increasing risk on our levels of service, staff, contractors and communities. The condition-based pump overhaul programme is also delivering real financial benefits, with around $398,000 saved and $648,000 deferred since 2019.
The team is now applying a similar proactive approach to its motors. More than 220 of them keep the scheme running and while the standard life expectancy for motors is 25 years, many are 50 to 60 years old and highly inefficient. Due to their unusual nature (old imperial dimensions, very low speed and large kilowatts), the motors tend to have very long lead times of four to five months. As a result, rebuilding is quicker than replacing a failed one. However, this lowers the efficiency of the motors further and also makes them more likely to fail in the future.
The motor resilience project is long term. Over the next 10 to 20 years, the team is working to replace old motors with modern metric equivalents. A lot of work is done up front to proactively change four motors per year and the transition frees up spares that can cover other motors in the scheme. This project not only improves the reliability of our assets; it creates higher efficiencies too. An average site can save up to $1400 per year on power and once all motors are replaced, we expect to save over $200,000 per year.
This work is part of ongoing efforts to improve the efficiency and resilience of our flood protection systems. Steve says most people across the Waikato don’t even know the flood protection schemes exist. If the schemes are working well everyone stays dry and the rivers move the flood waters out to sea. It’s when something goes wrong that people notice. Our teams will keep working hard to improve the reliability of the scheme and when failures do occur, we have built in sufficient resilience to get them back running again in the shortest possible time.
To ask for help or report a problem, contact us
Tell us how we can improve the information on this page. (optional)